Страсти по БТРам: в чем главная проблема украинской оборонки
Почему бронетанковые заводы попадают в скандалы
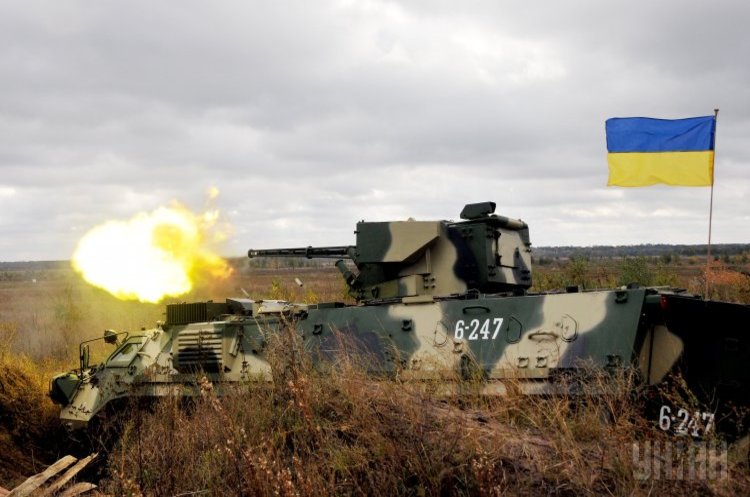
За годы независимости Украины существовало не так много удачных проектов в военно-промышленной сфере. И одним из поводов для гордости было разворачивание «с нуля» производства в стране легкой бронетехники – прежде всего бронетранспортеров. До 2014 года считалось вполне естественным, что эта техника пользовалась устойчивым спросом на международном рынке и ее не было на вооружении украинской армии, которая довольствовалась БТР-70 и БТР-80 предыдущего поколения. А первыми новейшими бронетранспортерами на вооружении НГУ и армии стали БТР-4 из иракского заказа и БТР-3 – из тайского.
Из-за того, что серийное производство было развернуто на полную мощность, в околовоенных кругах царила уверенность, что насыщение новой техникой частей ВСУ пойдет достаточно быстрыми темпами. Однако практически сразу «бронетранспортерная» программа забуксовала. Причем до такой степени, что, несмотря на огромные суммы, выделяемые из государственного бюджета, производители были вынуждены платить штраф и пени «за несвоевременное исполнение контрактов, заключенных с воинскими формированиями» – как это было совсем недавно с ГП «Киевский бронетанковый завод».
И это во время активной фазы войны и того, что в некоторых подразделениях до сих пор основным средством передвижения пехоты являются совсем уж древние БТР-60 крайне неудачной конструкции. Почему так произошло, специально для Mind анализирует военный эксперт Михаил Жирохов.
Как производятся украинские БТРы? По состоянию на 2014 год все производство как БТР-3, так и БТР-4 зависело от одного производителя бронекорпусов – частного предприятия «Лозовский кузнечно-механический завод». Причем производство шло (и идет) по технологии, освоенной еще во время Советского Союза. Для понимания ее крайней устарелости и огромной трудозатратности в двух словах опишем технологический процесс производства бронекорпуса.
Итак, закупается листовая, что важно – закаленная определенным образом, броневая сталь. Она режется по шаблонам, зачищается кромка, а затем бригада сварщиков на специальных стапелях сваривает сам корпус. Потом эта заготовка загружается в гигантскую печь, где корпус по определенной технологии закаливается до нужной температуры и затем постепенно охлаждается.
При этом результат зависит от многих факторов. И, как показывает опыт, хорошо получается не всегда. Так, было, например, в 2013 году, когда Ирак отказался от целой партии БТР-4 именно из-за трещин в броне. В той ситуации, конечно, была большая доля российского антипиара нашей оборонки, но не стоит отрицать и реальные проблемы.
В чем главные сложности? Сам процесс производства корпуса очень долгий, он предполагает достаточно высокую квалификацию сварщиков, большое количество ручного труда и как итог – достаточно высокая стоимость бронекорпуса. В итоге максимум, которого на пике своих возможностей могло достигать предприятие – это двадцать корпусов в месяц.
При том, что в большинстве стран от такой технологии уже давно отошли. На современных бронетранспортерах корпуса свариваются сразу из закаленной брони, причем выполняют эту работу аппараты роботизированной линии, а не люди.
А именно люди в нашем случае оказались одним из самых проблемных звеньев всей технологической цепочки. Потому что, когда Министерство обороны Украины «созрело» до заказа бронетранспортеров достаточно большими партиями (как любят говорить генералы – «батальонными комплектами»), то оказалось, что в Лозовой просто некому выполнять эти мега-заказы.
По состоянию на 2018 год из нескольких бригад сварщиков образца 2014 года проводить работы по корпусам могла лишь одна. Этому было сразу несколько причин – и тотальное безденежье, которое на фоне возможности поработать в Европе оказалось очень важным фактором утечки кадров, и просто старение персонала (за годы независимости потребность в таком количестве сварщиков просто отсутствовала, и система профтехподготовки их столько не выпускала – не было рабочих мест).
Все это привело к тому, что государственный заказ полностью оказался под угрозой срыва. И пришлось в экстренном порядке что-то предпринимать. С начала 2018 года в Лозовую в авральном порядке была откомандирована бригада квалифицированных сварщиков из Харькова – то есть государственный ХКБМ был вынужден помогать частному ЛКМЗ. Это в какой-то мере позволило стабилизировать ситуацию, однако очевидно, что это временное решение.
Помимо этого «Укроборонпром» принял решение развернуть самостоятельное производство корпусов БТР на собственных мощностях, чтобы не зависеть от Лозовой. Были выделены финансы и начаты работы на Киевском бронетанковом заводе, на ХКБМ и на харьковском заводе имени Малышева.
Но тут из-за недостатка финансов пошли по самому простому пути – простого клонирования советского технологического производства «а-ля Лозовая». То есть перехода на качественно новый уровень не произошло и в ближайшее время даже не предвидится. Таким образом украинский военно-промышленный комплекс сам себя загнал в тупик.
Как выйти из этого тупика? Наиболее перспективным видится путь сотрудничества с иностранными производителями в плане локализации бронетранспортера совместного производства с широким использованием отечественных наработок, а также узлов и агрегатов. Ведь очевидно, что перестроить производство под нынешнюю конструкцию просто нереально – например, корпус того же БТР-3 состоит из такого количества элементов, которые воспроизвести с помощью роботизированной техники настолько проблематично, что проще спроектировать новый.
Таким образом, можно говорить о том, что проблема с заменой парка бронетранспортеров советского производства для украинской армии останется актуальной как минимум ближайшие лет пять. К тому же, вариантов разработки нового перспективного образца пока не просматривается. А уже стоило бы задуматься – прогресс не стоит на месте, а технологическое отставание отечественной военной промышленности с каждым годом только увеличивается.
Причем касается этой всей цепочки производителей – например, пока так и не удалось использовать броневую сталь местного (мариупольского) производства. Дело в том, что она не проходит полный цикл термообработки, потому при производстве корпусов бронетранспортеров возникает дополнительный технологический этап в виде дозакаливания брони. В итоге после просчетов экономисты пришли к выводу, что с такими расходам энергоресурсов дешевле покупать уже готовую сталь бельгийского производства.
Поэтому все проблемы, возникающие в производстве БТРов, как в капле воды отражают все перекосы отечественной оборонки – начиная от нехватки квалифицированных кадров до технологической отсталости производства.
За годы независимости Украины было не так много удачных проектов в военно-промышленной сфере. И одним из поводов для гордости было разворачивание «с нуля» производства в стране легкой бронетехники – прежде всего бронетранспортеров. До 2014 года было вполне естественным, что эта техника пользовалась устойчивым спросом на международном рынке и ее не было на вооружении украинской армии, которая довольствовалась БТР-70 и БТР-80 предыдущего поколения. А первыми новейшими бронетранспортерами на вооружении НГУ и армии стали БТР-4 из иракского заказа и БТР-3 – из тайского.
Из-за того, что серийное производство было развернуто на полную мощность, в околовоенных кругах царила уверенность, что насыщение новой техникой частей ВСУ пойдет достаточно быстрыми темпами. Однако практически сразу «бронетранспортерная» программа забуксовала. Причем до такой степени, что, несмотря на огромные суммы, выделяемые из государственного бюджета, производители были вынуждены платить штраф и пени «за несвоевременное исполнение контрактов, заключенных с воинскими формированиями» – как это было совсем недавно с ГП «Киевский бронетанковый завод».
И это во время активной фазы войны и того, что в некоторых подразделениях до сих пор основным средством передвижения пехоты являются совсем уж древние БТР-60 крайне неудачной конструкции. Почему так произошло, специально для Mind анализирует военный эксперт Михаил Жирохов.
Как производятся украинские БТРы? По состоянию на 2014 год все производство как БТР-3, так и БТР-4 зависело от одного производителя бронекорпусов – частного предприятия «Лозовский кузнечно-механический завод». Причем производство шло (и идет) по технологии, освоенной еще во время Советского Союза. Для понимания ее крайней устарелости и огромной трудозатратности в двух словах опишем технологический процесс производства бронекорпуса.
Итак, закупается листовая, что важно – закаленная определенным образом, броневая сталь. Она режется по шаблонам, зачищается кромка, а затем бригада сварщиков на специальных стапелях сваривает сам корпус. Потом эта заготовка загружается в гигантскую печь, где корпус по определенной технологии закаливается до нужной температуры и затем постепенно охлаждается.
При этом результат зависит от многих факторов. И, как показывает опыт, хорошо получается не всегда. Так, было, например, в 2013 году, когда Ирак отказался от целой партии БТР-4 именно из-за трещин в броне. В той ситуации, конечно, была большая доля российского антипиара нашей оборонки, но не стоит отрицать и реальные проблемы.
В чем главные сложности? Сам процесс производства корпуса очень долгий, он предполагает достаточно высокую квалификацию сварщиков, большое количество ручного труда и как итог – достаточно высокая стоимость бронекорпуса. В итоге максимум, которого на пике своих возможностей могло достигать предприятие – это двадцать корпусов в месяц.
При том, что в большинстве стран от такой технологии уже давно отошли. На современных бронетранспортерах корпуса свариваются сразу из закаленной брони, причем выполняют эту работу аппараты роботизированной линии, а не люди.
А именно люди в нашем случае оказались одним из самых проблемных «узлов» всей технологической цепочки. Потому что, когда Министерство обороны Украины «созрело» до заказа бронетранспортеров достаточно большими партиями (как любят говорить генералы – «батальонными комплектами»), то оказалось, что в Лозовой просто некому выполнять эти мега-заказы.
По состоянию на 2018 год из нескольких бригад сварщиков образца 2014 года проволить работы по корпусам могла лишь одна. Этому было сразу несколько причин – и тотальное безденежье, которое на фоне возможности поработать в Европе, оказалось очень важным фактором утечки кадров, и просто старение персонала (за годы независимости потребность в таком количестве сварщиков просто отсутствовала, и система профтехподготовки их столько не выпускала – не было рабочих мест).
Все это привело к тому, что государственный заказ полностью оказался под угрозой срыва. И пришлось в экстренном порядке что-то предпринимать. С начала 2018 года в Лозовую в авральном порядке была откомандирована бригада квалифицированных сварщиков из Харькова – то есть государственный ХКБМ был вынужден помогать частному ЛКМЗ. Это в какой-то мере помогло стабилизировать ситуацию, однако очевидно, что это временное решение.
Помимо этого «Укроборонпром» принял решение развернуть самостоятельное производство корпусов БТР на собственных мощностях, чтобы не зависеть от Лозовой. Были выделены финансы и начаты работы на Киевском бронетанковом заводе, на ХКБМ и на харьковском заводе имени Малышева.
Но тут из-за недостатка финансов пошли по самому простому пути – простого клонирования советского технологического производства «а-ля Лозовая». То есть перехода на качественно новый уровень не произошло и в ближайшее время даже не предвидится. Таким образом украинский военно-промышленный комплекс сам себя загнал в тупик.
Как выйти из этого тупика? Наиболее перспективным видится путь сотрудничества с иностранными производителями в плане локализации бронетранспортера совместного производства с широким использованием отечественных наработок, а также узлов и агрегатов. Ведь очевидно, что перестроить производство под нынешнюю конструкцию просто нереально – например, корпус того же БТР-3 состоит из такого количества элементов, которые воспроизвести с помощью роботизированной техники настолько проблематично, что проще спроектировать новый.
Таким образом, можно говорить о том, что проблема с заменой парка бронетранспортеров советского производства для украинской армии останется актуальной как минимум ближайшие лет пять. К тому же, вариантов разработки нового перспективного образца пока не просматривается. А уже стоило бы задуматься – прогресс не стоит на месте, а технологическое отставание отечественной военной промышленности с каждым годом только увеличивается.
Причем касается этой всей цепочки производителей – например, пока так и не удалось использовать броневую сталь местного (мариупольского) производства. Дело в том, что она не проходит полный цикл термообработки, потому при производстве корпусов бронетранспортеров возникает дополнительный технологический этап в виде дозакаливания брони. В итоге после просчетов экономисты пришли к выводу, что с такими расходам энергоресурсов дешевле покупать уже готовую сталь бельгийского производства.
Поэтому все проблемы, возникающие в производстве БТРов, как в капле воды отражают все перекосы отечественной оборонки – начиная от нехватки квалифицированных кадров до технологической отсталости производства.
Авторы материалов OpenMind, как правило, внешние эксперты и специалисты, которые готовят материал по заказу редакции. Но их точка зрения может не совпадать с точкой зрения редакции Mind.
В то же время редакция несёт ответственность за достоверность и соответствие реальности изложенной мысли, в частности, осуществляет факт-чекинг приведенных утверждений и первичную проверку автора.
Mind также тщательно выбирает темы и колонки, которые могут быть опубликованы в разделе OpenMind, и обрабатывает их в соответствии со стандартами редакции.