Пристрасті за БТРами: у чому головна проблема української оборонки
Чому бронетанкові заводи потрапляють у скандали
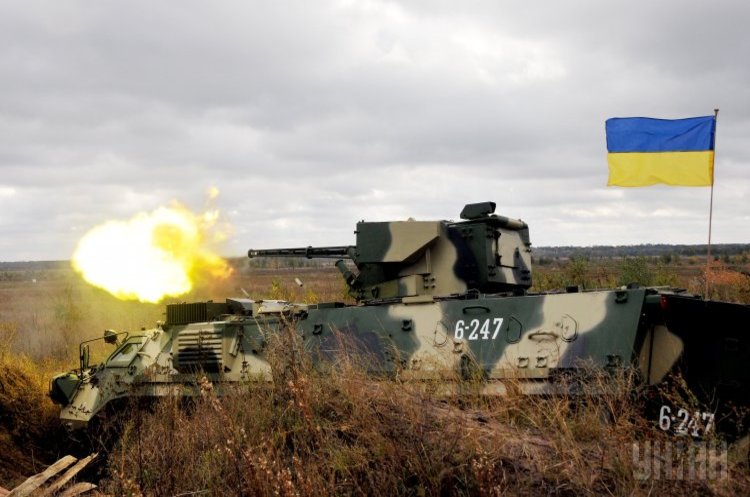
За роки незалежності України існувало не надто багато вдалих проектів у військово-промисловій сфері. І одним із приводів для гордості було розгортання «з нуля» виробництва в країні легкої бронетехніки – перш за все бронетранспортерів. До 2014 року вважалося цілком природним, що ця техніка користувалася стійким попитом на міжнародному ринку, і її не було на озброєнні української армії, яка задовольнялася БТР-70 і БТР-80 попереднього покоління. А першими новітніми бронетранспортерами на озброєнні НГУ і армії стали БТР-4 з іракського замовлення і БТР-3 – з тайського.
Через те що серійне виробництво було розгорнуто на повну потужність, у навколовійськових колах панувала впевненість, що насичення новою технікою частин ЗСУ піде досить швидкими темпами. Однак практично відразу «бронетранспортерна» програма забуксувала. Причому до такої міри, що, незважаючи на величезні суми, які виділяються з державного бюджету, виробники були змушені платити штраф і пені «за несвоєчасне виконання контрактів, укладених з військовими формуваннями» – як це було зовсім нещодавно з ДП «Київський бронетанковий завод».
І це під час активної фази війни і того, що в деяких підрозділах й досі основним засобом пересування піхоти є зовсім вже стародавні БТР-60 вкрай невдалої конструкції. Чому так сталося, спеціально для Mind аналізує військовий експерт Михайло Жирохов.
Як виробляються українські БТРи? Станом на 2014 рік усе виробництво як БТР-3, так і БТР-4 залежало від одного виробника бронекорпусів – приватного підприємства «Лозовський ковальсько-механічний завод». Причому виробництво йшло (і йде) за технологією, освоєною ще за часів Радянського Союзу. Для розуміння її крайньої застарілості та величезної трудомісткості коротко опишемо технологічний процес виробництва бронекорпусу.
Отже, закуповується листова, що важливо – загартована певним чином, броньована сталь. Вона ріжеться по шаблонах, зачищається кромка, а потім бригада зварювальників на спеціальних стапелях зварює сам корпус. Потім ця заготовка завантажується в гігантську піч, де корпус за певною технологією гартується до потрібної температури і потім поступово охолоджується.
При цьому результат залежить від багатьох факторів. І, як показує досвід, добре виходить не завжди. Так було, наприклад, у 2013 році, коли Ірак відмовився від цілої партії БТР-4 саме через тріщини в броні. У тій ситуації, звичайно, була велика частка російського антипіару нашої оборонки, але не варто заперечувати і реальні проблеми.
У чому головні труднощі? Сам процес виробництва корпусу дуже довгий, він передбачає досить високу кваліфікацію зварників, велику кількість ручної праці та в підсумку – дає досить високу вартість бронекорпусу. В результаті максимум, якого на піку своїх можливостей могло досягати підприємство – це 20 корпусів на місяць.
При тому що в більшості країн від такої технології вже давно відійшли. На сучасних бронетранспортерах корпуси зварюються відразу з загартованої броні, причому виконують цю роботу апарати роботизованої лінії, а не люди.
А саме люди в нашому випадку виявилися однією із найпроблемніших ланок усього технологічного ланцюжка. Бо коли Міністерство оборони України «дозріло» до замовлення бронетранспортерів досить великими партіями (як полюбляють говорити генерали – «батальйонними комплектами»), то виявилося, що в Лозовій просто нема кому виконувати ці мегазамовлення.
Станом на 2018 рік з декількох бригад зварників зразка 2014 року проводити корпусні роботи могла лише одна. Одразу через декілька причин: і тотальне безгрошів'я, яке на тлі можливості попрацювати в Європі виявилося дуже важливим фактором витоку кадрів, і просто старіння персоналу (за роки незалежності потреби в такій кількості зварників просто не було, і система профтехпідготовки їх стільки не випускала – не було робочих місць).
Все це призвело до того, що державне замовлення повністю опинилося під загрозою зриву. І довелося в екстреному порядку щось робити. З початку 2018 року до Лозової в авральному порядку було відряджено бригаду кваліфікованих зварників з Харкова – тобто державний ХКБМ був змушений допомагати приватному ЛКМЗ. Це якоюсь мірою дозволило стабілізувати ситуацію, однак очевидно, що це тимчасове рішення.
Крім цього «Укроборонпром» вирішив розгорнути самостійне виробництво корпусів БТР на власних потужностях, щоб не залежати від Лозової. Були виділені фінанси і розпочато роботи на Київському бронетанковому заводі, на ХКБМ і на харківському заводі імені Малишева.
Але тут через нестачу фінансів пішли найпростішим шляхом – простого клонування радянського технологічного виробництва «а-ля Лозова». Тобто переходу на якісно новий рівень не відбулося і найближчим часом навіть не передбачається. Таким чином український військово-промисловий комплекс сам себе загнав у глухий кут.
Як вийти з цього глухого кута? Найперспективнішим бачиться шлях співпраці з іноземними виробниками в плані локалізації бронетранспортера спільного виробництва з широким використанням вітчизняних напрацювань, а також вузлів і агрегатів. Адже очевидно, що перебудувати виробництво під нинішню конструкцію просто нереально – наприклад, корпус того ж БТР-3 складається з великої кількості елементів, які відтворити за допомогою роботизованої техніки так проблематично, що простіше спроектувати новий.
Таким чином, проблема із заміною парку бронетранспортерів радянського виробництва для української армії залишиться актуальною як мінімум у найближчі років п'ять. До того ж варіантів розробки нового перспективного зразка поки не проглядається. А вже варто було б замислитися – прогрес не стоїть на місці, а технологічне відставання вітчизняної військової промисловості з кожним роком лише збільшується.
Причому стосується це всього ланцюжка виробників – наприклад, поки так і не вдалося використати броньовану сталь місцевого (маріупольського) виробництва. Справа в тому, що вона не проходить повний цикл термообробки, тому при виробництві корпусів бронетранспортерів виникає додатковий технологічний етап у вигляді дозагартування броні. У підсумку після прорахунків економісти дійшли висновку, що з такими витратами енергоресурсів дешевше купувати вже готову сталь бельгійського виробництва.
Тому всі проблеми, що виникають у виробництві БТРів, як у краплі води відбивають усі перекоси вітчизняної оборонки – починаючи від браку кваліфікованих кадрів до технологічної відсталості виробництва.
Автори матеріалів OpenMind, як правило, зовнішні експерти та дописувачі, що готують матеріал на замовлення редакції. Але їхня точка зору може не збігатися з точкою зору редакції Mind.
Водночас редакція несе відповідальність за достовірність та відповідність викладеної думки реальності, зокрема, здійснює факт-чекінг наведених тверджень та первинну перевірку автора.
Mind також ретельно вибирає теми та колонки, що можуть бути опубліковані в розділі OpenMind, та опрацьовує їх згідно зі стандартами редакції.