Інновації в металургії: як «цифра» запобігає «втомі металу»
Екологія, імідж чи продуктивність – що спонукає сталеварів до запровадження нових технологій?
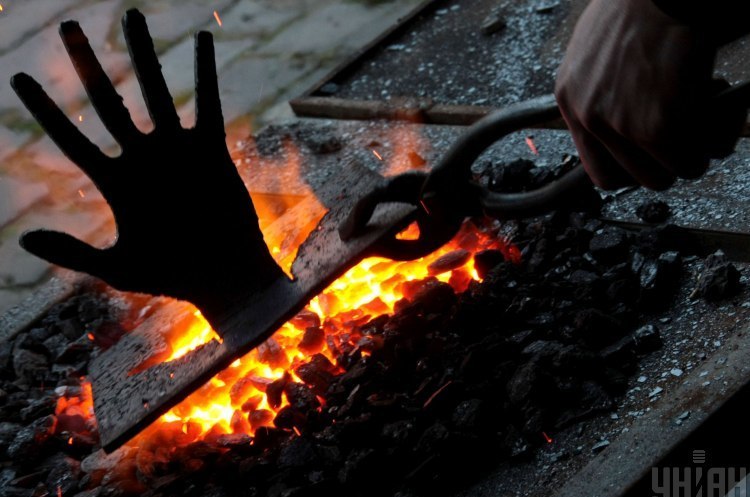
Mind.ua в партнерстві з платформою відкритих інновацій Re:actor і компанією KPMG в Україні готує перший у країні Індекс інноваційності українського бізнесу. Ми хочемо зрозуміти, наскільки найпотужніші галузі економіки готові до викликів майбутнього, які інновації впроваджують найбільші гравці та куди рухається ринок. Результати оцінки компаній будуть озвучені 10 жовтня на конференції Tech Fusion 2019 і опубліковані на Mind.
Ми вже писали, що відбувається, коли один з найконсервативніших секторів – агро – об'єднує свої зусилля з високими технологіями, яких змін зазнає банківська сфера з приходом у неї новітніх технологічних розробок, як інновації впливають на телеком-сегмент і наскільки інноваційною є будівельна галузь. Тепер пропонуємо зупинитися на тому, як технологічний прогрес змінює «правила гри» для металургів.
Металургія, нарівні з агросектором і паливно-енергетичним комплексом, – одна з найбільш консервативних галузей економіки. Тому інновації тут запроваджуються лише точково, і спрямовані вони здебільшого на вдосконалення класичних процесів виробництва.
Що нового в світі?
Виробництво металу не зазнало принципових змін відтоді, як людство його винайшло кілька тисяч років тому. Збагачення руди – виплавка чавуну в доменних печах – виробництво металу у мартенах або конвертерах – лиття заготовок на спеціальних прокатних станах – виробництво металургійної продукції з заготовок. Кожен з цих етапів шкідливий для довкілля, енергоємний, небезпечний для працівників відповідних підприємств.
У прогресивних металургійних колах вже давно обговорюють принципово нову технологію, а саме – виробництво залізорудної сировини та, власне, металу за допомогою водню. Подекуди, цю технологію вже застосовують при збагаченні руди, але запроваджувати її на комбінатах не поспішають через надмірну дорожнечу. І так буде ще років 25-30.
Ще у 50-х роках минулого століття розвинені країни замінили старі мартеновські печі на більш прогресивні та екологічніші конвертери. На жаль, ця тенденція не стала домінуючою в Україні – майже всі вітчизняні метзаводи працюють одночасно як на тих, так і на інших. І позбуватися мартенів найближчим часом не планують.
Відповідно до рейтингу виробництва сталі, який складає Всесвітня асоціація виробників сталі (Worldsteel), абсолютним лідером є Китай – він за серпень поточного року виплавив 87,2 млн тонн цього металу. Усі інші країни навіть не наближаються до КНР. Індія, що посідає друге місце, виробила лише 9,3 млн тонн; США (4-те місце) – 7,5 млн тонн; Росія (6-те місце) – 5,9 млн тонн. До рейтингу включені 64 країни – основні світові виробники цієї продукції.
Чи прижилися інновації в українській металургії?
Україна наразі піднялася на 11 місце у рейтингу Worldsteel з показником у 1,9 млн тонн виплавленої сталі. Тут варто зауважити, що до 2014 року вітчизняні металурги входили до першої десятки списку, та за роки війни на Донбасі «скотилися» аж на 13 місце, і лише у серпні 2019-го дещо покращили свої позиції.
Разом із тим, експорт чорних металів з України забезпечує понад 20% валютної виручки, або майже $10 млрд на рік. Та за вісім місяців нинішнього року країна знизила експорт на 10%, через погану кон’юнктуру на світових ринках металу. Ціни на прокат і металургійну продукцію знижуються, заводи втрачають рентабельність. Виходом із цієї ситуації є саме впровадження інновацій та модернізація, які зменшують собівартість продукції.
При цьому дійсно сучасний метзавод в Україні лише один – «Інтерпайп Сталь». Його було побудовано «з нуля» у 2012 році, вартість будівництва склала $700 млн. На заводі працюють виключно електродугові печі, а основна сировина – металобрухт. Усі процеси максимально автоматизовані, керуються та контролюються за допомогою MES-системи, програмного забезпечення італійської компанії Danieli, яке дозволяє оптимізувати процес виробництва і трудовитрати.
Усі інші українські металургійні заводи запроваджують інновації у трьох напрямках:
- встановлюють нове сучасне обладнання;
- модернізують старе з обов’язковим запровадженням нових екологічних систем і вдосконалюють виробничі процеси, щоб збільшити сортамент продукції;
- впроваджують цифрові технології на усіх етапах виробництва.
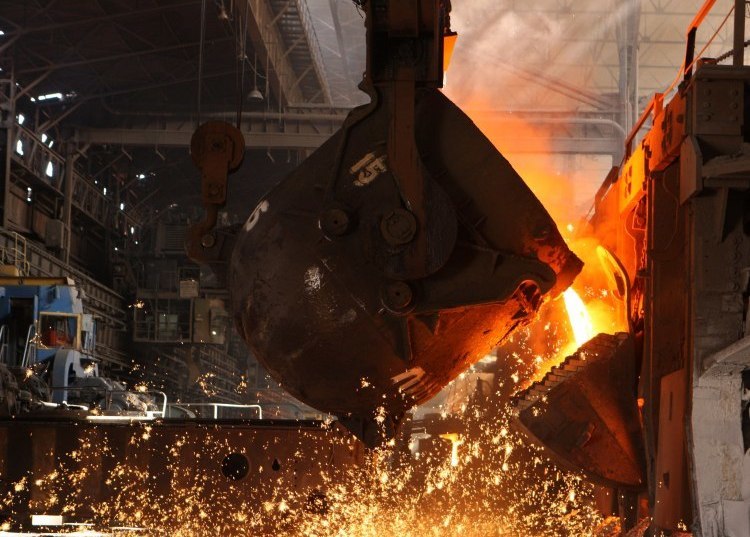
Ливарний цех
Скільки коштує модернізація?
Усі українські підприємства, проводячи реконструкцію, звітують і про екологічні вдосконалення, оскільки постачають свою продукцію на західні ринки. Еко-складова для експорту дуже важлива: за викиди доводиться платити екологічний податок, тож, чим менше викидів – тим менша собівартість. А у взаєминах із зарубіжними партнерами це ще й іміджеве питання.
Цього року комбінат ім. Ілліча (Маріуполь) запустив нову машину безперервного лиття заготовок №4 (МБЛЗ №4), вартість проекту склала $150 млн. У певному сенсі ця новація стала «кроком на випередження»: фільтри, встановлені у цеху, вловлюють виробничий пил у чотири рази активніше, ніж вимагає українське законодавство. Це важливий аспект, адже Маріуполь – одне з найбруднішим міст України. У комплекс також входить установка позапічної обробки сталі, яка дозволяє зробити майже будь-яку марку цього металу, в тому числі і для виробництва труб.
«ArcelorMittal Кривий Ріг» до кінця року планує добудувати дві машини безперервного лиття – №2 і №3. А поки що запустив гаряче випробування реконструйованого дрібносортового стану-250-4. Потужність стану зросте з 800 000 до 1,04 млн тонн на рік, а викиди знизяться на 131 тонну. Вартість реконструкції склала $50 млн. Загалом, у найближчі п’ять років ArcelorMittal планує скерувати на розвиток виробництва $1,8 млрд. Серед головних проектів – будівництво фабрики окатишів. Вона дозволить відмовитися від застарілого виробництва агломерату та зменшить небезпечні викиди на 50-55%.
«Запоріжсталь» провела модернізацію газоочисних систем агломашин №1-6 вартістю 1,2 млрд грн., що дало зниження викидів пилу на 90%, а оксидів сірки – на 50%. На кожній машині встановлено датчик контролю викидів та систему онлайн-моніторингу, завдяки яким є змога оперативно керувати процесом очищення. Також на заводі реалізовано інтелектуальну модель доменної печі із застосуванням технології лазерного сканування сегментів та крупновузлової збірки агрегатів. Нову піч збудували за вісім місяців замість «стандартних» двох років, а викиди пилу з неї становлять лише 20 мг на кубометр.
Реконструкцію із встановленням сучасного обладнання провели і на комбінаті «Азовсталь»: доменна піч-3, система газоочищення установки піч-ковш-1,2; система паровидалення МБЛЗ-5. У Донецькій області діє екологічна програма обласної держадміністрації, яка слідкує за її виконанням.
Сьогодні металургійні підприємства змушені швидко реагувати на зміни кон’юнктури ринку. Тож, окрім вирішення екологічних завдань, реконструкція та модернізація обладнання дозволяють оптимізувати витрати на виробництво продукції і запровадити випуск нових видів.
Наприклад, «Азовсталь» заради цього провела заміну корпуса конвертера, збудувала установку для пило-вугільного палива, реконструювала міксерне та дробильне відділення у конвертерному цеху.
Майже 3 млн грн вклав у капітальний ремонт конвертера №1 Дніпровський металургійний комбінат (Кам’янське, Дніпропетровської області). Головна задача – подовження терміну експлуатації. Також цієї осені в прокатному цеху почалося освоєння нового процесу – сліттінгу (Slitting). Ця технологія дозволяє інтенсифікувати випуск продукції, знизити витрати енергії на 10-30%, знизити витрати металу та на 25% підвищити продуктивність прокатного стану.
Як і де машини конкурують із людьми?
Найцікавішими інноваціями на метзаводах є запровадження цифрових продуктів, які максимально скорочують вплив людського фактору. Так, на «Запоріжсталі» фінансова дирекція разом із ІТ-службою комбінату розробили універсальну платформу обробки документації: до інформаційної системи комбінату під’єднали високошвидкісні потокові сканери в комплексі з програмним продуктом ABBYY FlexiCapture. Відтак уся текстова та графічна інформація «оцифровується» в автоматизованому режимі, значно зменшивши ризик помилок при введенні даних вручну. Витрати на обробку документів скоротилися на 50%, а швидкість вводу даних в інформаційну систему зросла у 5-10 разів.
Також на «Запоріжсталі» запустили систему «Мобільний світлофор» – для оперативного моніторингу виробничих процесів. У цеху гарячої прокатки тонкого листа в пілотному режимі встановлено 2 000 датчиків, з яких можна зчитати 130 000 параметрів роботи обладнання. Програма дає можливість оперативно приймати рішення про своєчасне виконання необхідних ремонтних робіт. Враховується процент зношеності, періодичність заміни деталей, термін експлуатації, швидкість розвитку дефекту тощо. Принцип роботи системи передбачає збирання та занесення в єдину електронну базу даних про стан обладнання у всіх цехах.
Якщо раніше робітники спочатку проводили огляд обладнання, а потім вносили відомості у систему через персональний комп’ютер, то з мобільним управлінням (в рамках проекту «Мобільний світлофор») інформація передається безпосередньо під час огляду. При підтвердженні очікуваного ефекту проект планується реалізувати і в інших виробничих цехах комбінату – агломераційному, доменному, мартеновскому, обжимному і ЦХП №1.
Приблизно така ж система працює на заводі «Інтерпайп Сталь» з 2016 року. Це модуль Smart.EAM – для технічного обслуговування та ремонту обладнання. Його розробник – українська компанія IT-Enterprise. В систему внесено усю інформацію про основне обладнання заводу, включаючи креслення. Кожен великий агрегат розписаний до найдрібніших деталей. Стан важливих вузлів регулярно моніториться за допомогою контролерів та датчиків.
Система накопичує інформацію про стан кожного вузла, простої обладнання, зауваження персоналу, аналізує їх та прогнозує, коли деталь вийде з ладу. Це дозволяє швидко замінити проблемні деталі та не допустити простою обладнання, або ж – не витрачати кошти на заміну, якщо деталь не зношена і функціонує в нормальному режимі.
Модуль Smart.EAM допомагає не лише в обслуговуванні обладнання, а й у плануванні закупки ТМЦ. Зокрема, за його допомогою створено карти ремонтів кожного вузла, і спеціаліст може визначити, що й коли міняти. У результаті кількість аварій на виробництві знизилася з 2% до 0,3%, а обсяг бракованої продукції при аварійній зупинці обладнання зменшився усемеро. кількість. Запаси деталей на складі знизилися на 10%, а загальна ефективність роботи обладнання зросла на 10-15%.
Сьогодні «Інтерпайп» впроваджує ще одну систему – Smart. Factory – проєкт з наскрізного відслідковування та планування виробництва. Це важливо, коли завод виробляє спочатку заготовку, а потім і продукцію з різних марок сталі. Система будується на основі технології промислового інтернету речей (ІоТ) – інформація про кожен продукт (наприклад: номер плавки, марка сталі, номер замовлення і т.д.) зберігається в єдиній базі даних.
Перед відвантаженням заготовки на кожну прикріплюють спеціальну бірку з QR-кодом, і спеціалісти таким чином ведуть облік на складі. При постачанні заготовки у виробничі цехи QR-код сканується і автоматично завантажується в систему управління обладнанням, і формуються виробничі завдання. Готова продукція відвантажується також із біркою з QR-кодом, клієнт при скануванні може побачити онлайн всю інформацію.
«Інтерпайп» випробовує цю систему при виробництві труб, але її можна пристосувати до будь-якого підприємства. І, вірогідно, найближчим часом такі модулі з’являться й на інших металургійних заводах.
Якщо ви дочитали цей матеріал до кінця, ми сподіваємось, що це значить, що він був корисним для вас.
Ми працюємо над тим, аби наша журналістська та аналітична робота була якісною, і прагнемо виконувати її максимально компетентно. Це вимагає і фінансової незалежності.
Станьте підписником Mind всього за 196 грн на місяць та підтримайте розвиток незалежної ділової журналістики!
Ви можете скасувати підписку у будь-який момент у власному кабінеті LIQPAY, або написавши нам на адресу: [email protected].